While on a recent run I broke a half-shaft in my YA. In a recent article I alluded to having organised the manufacture of a batch for YA/YTs. The later YB back axles are different and common with TDs, hence half-shafts for these are readily available. For those of you who may not have read the previous article regarding how all this came about I'll cover it briefly. Generally I discovered that YA/YT half-shafts were like hens teeth to find. Being made from one piece, from a forged billet, is what makes them expensive. I decided therefore to examine the possibility of making them in two pieces, i.e. the flange and the shaft separately ("floating" similarly to the pre-war cars and the T types). The diagram below shows the original design.
Having noticed that there is a large space behind the hub caps (some 2 5/8 -a little over 66mm) and of a diameter a little smaller than the diameter of the wheel centre, it occurred to me that there was space enough to beef up the flange to take a splined shaft. Following discussion with the maker I was assured that a taper similar to that used on cars used for racing would be more than adequate and less expensive. The modified design ended up as the diagram below.
The photograph (Figure 1 below) shows the old and new half-shafts together. Apart from the extra block of material on the outer end, they are the same.
I took delivery of the first two and fitted them to my own car., The next two photo's (Figures 2 and 3 below) show how each look when installed.
Figures 4 and 5 below show what the difference is with the wheel removed.
Figures 6 and 7 below show the same with the brake drum removed.
Fitting them was quite straightforward with only one small challenge in that new grease nipples were required that have flats 3/8" across. The original ones with the large hexagon will not turn past the large nut on the outer end since the tapped hole is quite close to it.
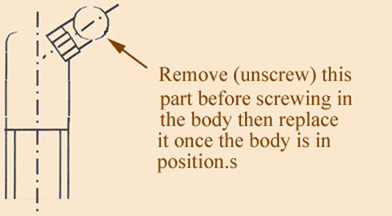
I had a couple of 45° grease nipples in my bits box. In order that they could turn I unscrewed the short angled piece that the grease gun fits before I screwed the body into the hole in the half shaft flange.
Once the body was in place with the angled hole pointing so that a grease gun would fit on without fouling the hub nut, I replaced the small angled piece (see figure 8). Since fitting the new half-shafts I've driven a few miles and so far all seems well.
Necessity caused me to organise the manufacture of these and at the same time I had more made which the MG Octagon Car Club kindly funded. 24 were made of which I had two and the remainder are available from the MG Octagon Car Club Spares, so contact them if you want some. In the event that they become used up we now know where we can go to get more made. Let's keep-em-rollin' |